- +86-15770741413
- sales6@klspcba.com
- Building 4, Shayi Beifang Technology Park, Baoan District, Shenzhen
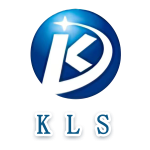
Menu
Here are some key points and best practices when performing hardware BMS (Battery Management System) testing:
– A BMS HIL test system is a high-performance platform that provides all the necessary input signals for simulating a battery pack. The real-time operating system executes complex battery cell and pack models that are commonly used for BMS algorithm development and firmware regression testing.
– Capable of simulating the voltages of over 200 series-connected battery cells and pack voltage simulation up to 1000 VDC. In addition, current and temperature sensors can be simulated, as well as BMS control IOs and communications.
– The HIL test system supports fault insertion and auxiliary system measurements are critical for testing the response of the BMS under various fault conditions.
– Supports customized battery cell and pack model integration in Simulink, C++, LabVIEW, and other environments to suit specific test requirements.
– Provide software applications for manual operation, automated testing and report generation to facilitate control and management of the testing process.
– dSPACE offers a BMS test solution with a modular and scalable system architecture for any use case. The solution supports overall system voltages up to 1500V and can be used in a wide range of industries including automotive, aerospace, railroad, off-highway and energy.
– dSPACE offers solutions for testing BMSs at the signal level and at high voltage levels. Signal-level testing involves testing the main functions of the BMS and its interaction with the vehicle network or other environments without using high voltages. High voltage level testing involves testing the complete BMS, including one or all of the battery cell supervisory circuits (CSC modules), which is critical for release and acceptance testing.
– Modern BMS test systems contain high-resolution sensors capable of detecting small changes in parameters such as voltage, current, and temperature. These sensors are used where detailed battery status information is required so that the system can monitor or interface with the battery more effectively.
– Calibration is a critical process to maintain the accuracy of the BMS test system and should be maintained and calibrated regularly using accurate standards.
– Today’s BMS test systems also incorporate sophisticated data logging and analysis capabilities that allow you to capture, store and analyze large amounts of data over time.
– Some of the best practices to follow to ensure high accuracy in BMS testing include frequent calibration and maintenance of sensors, optimization of environmental conditions, regular software updates, and use of redundant data collection methods.
By following these key points and best practices, the effectiveness and accuracy of hardware BMS testing can be ensured, resulting in improved battery system performance and safety.
Manager:Nora Zeng
Wechat :15770741413
Whatsapp/Tel :+86-15770741413
E-mail:sales6@klspcba.com
Copyright © 2023 Shenzhen Kinglisheng Electronics Co., Ltd All rights reserved.