- +86-15770741413
- sales6@klspcba.com
- Building 4, Shayi Beifang Technology Park, Baoan District, Shenzhen
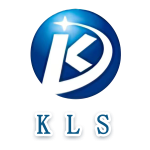
Menu
When conducting BMS (Battery Management System) testing, here are some key factors and best practices to ensure reliability and accuracy:
– Ensure that the BMS follows functional safety standards to prevent failures that could lead to unsafe conditions.
– Design the BMS with redundancy in mind to maintain operations even if a component fails.
– Verify that the BMS can withstand the environmental conditions to which it will be exposed during its lifetime.
– Verify that the BMS meets all relevant industry standards and regulations to ensure safety and effectiveness.
– Check the condition of the BMS test equipment to ensure that there is no damage that could affect functionality.
– Ensure that all cables and probes are properly connected and in good condition.
– Confirm that the power supply to the BMS test equipment is stable and reliable to avoid test interruption.
– Understand battery chemistry to accurately assess SOC and SOH.
– Monitor temperatures frequently to prevent performance degradation due to temperature extremes.
– Understand application-specific C rates to adjust BMS settings accordingly.
– Design the BMS to effectively manage extreme conditions such as overcharge, overheating, and rapid discharge.
– Implement strict quality control procedures to prevent voltage imbalance and ensure cell quality.
– To begin BMS testing, it is first necessary to simulate a large number of battery cells. This involves varying the cell output based on simulated environmental parameters to mimic real-world conditions.
– Set up the system to simulate the inputs and outputs of the battery monitoring circuitry (CSC), including temperature sensors, Hall effect sensors, and circuit parameters associated with the battery and contact relays. Ensure that all connections are secure and working as expected.
– Simulate a variety of operating conditions to evaluate the ability of the BMS to maintain safe and efficient battery operation under varying stressors and environmental influences.
– Perform a series of detailed tests including BMS communication tests, BMS safety tests, performance and reliability tests, and commercial BMS tests.
– Continuously monitor battery voltage and other key parameters throughout the testing process, collecting data using a multi-meter and specialized software such as KS8400A PathWave Test Automation to ensure a thorough evaluation.
– Ensure all safety measures are in place, especially when using lithium-ion batteries. Check for the presence of thermal fuses and ensure that the BMS contains appropriate protection such as short circuit, overcharge and discharge protection.
– Using the data collected, analyze the performance of the BMS in different scenarios to identify any potential design or manufacturing flaws and optimize the BMS design based on heat sink requirements, physical limitations, and the functional environment of the intended application.
By following these steps and taking these factors into consideration, BMS testing can be effectively conducted to ensure that the battery management system is safe, reliable, and performs optimally under all expected conditions.
Manager:Nora Zeng
Wechat :15770741413
Whatsapp/Tel :+86-15770741413
E-mail:sales6@klspcba.com
Copyright © 2023 Shenzhen Kinglisheng Electronics Co., Ltd All rights reserved.