- +86-15770741413
- sales6@klspcba.com
- Building 4, Shayi Beifang Technology Park, Baoan District, Shenzhen
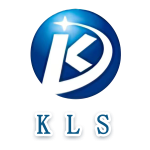
Menu
A Battery Electric Vehicle (BEV), Also known as a pure electric vehicle, only – electric vehicle, Or all – electric vehicle, Is a specific type of Electric Vehicles (EV). It solely relies on the chemical energy stored within rechargeable battery packs, Without any secondary means of propulsion. As a result, Battery electric vehicles do not feature an internal combustion engine, a fuel cell, Or a fuel tank. This category encompasses a wide range of vehicles, Including trucks, cars, buses, Motorcycles, bicycles, and forklifts. Various types of batteries are employed to power electric vehicles. The choice of the best battery depends on multiple factors such as energy storage efficiency, production costs, Construction characteristics, Safety, and lifespan. Among them, Lithium – ion batteries are the most commonly used technology in electric cars. Electric Vehicles operate on high – voltage Lithium – Ion battery packs. Compared to other battery chemistries, Lithium – ion batteries possess a higher energy density (ranging from 100 – 265wh/kg). However, They may pose a risk of fire under abnormal conditions. Therefore, It is of utmost importance to operate electric vehicles within predefined safety limits to safeguard both the user and the vehicle.
The three core technologies in electric vehicles are battery, Motor, And electronic control technology. These technologies play a crucial role as they are directly associated with the cruising range and acceleration performance of electric vehicles. Just like the barrel principle indicates, Any deficiency in one of these three technologies will have an immediate impact on the vehicle’s overall performance.
A Battery Management System (BMS), Which oversees the electronics of a rechargeable battery – whether it’s a single cell or a battery pack – emerges as a critical element in guaranteeing the safety of electric vehicles. It protects both the user and the battery by making sure that the cell operates within its safe operating parameters. The BMS keeps an eye on the State Of Health (SOH) of the battery, gathers data, Controls environmental factors influencing the cell, And balances them to ensure equal voltage among cells. A battery pack with a BMS connected to an external communication data transfer system or a data bus is known as a smart battery pack. It might incorporate additional features and functions, Such as fuel gauge integration, Smart bus communication protocols, General Purpose Input Output (GPIO) options, Cell balancing, wireless charging, Embedded battery chargers, And protection circuitry. All these are designed to offer information regarding the battery’s power status. This information can assist the device in conserving power in an intelligent manner. A smart battery pack can handle its own charging process, generate error reports, detect and inform the device of any low – charge situation, And predict the battery’s remaining lifespan or run – time. It also provides details about the cell’s current, voltage, And temperature and continuously self – corrects any errors to uphold its prediction accuracy. Smart battery packs are typically designed for use in portable devices like laptops and feature embedded electronics that enhance the battery’s reliability, safety, Lifespan, And functionality. These attributes facilitate the development of user – friendly and more reliable end products. For example, With embedded chargers, Batteries can have longer life cycles since the chargers charge the batteries to optimal and ideal specifications within temperature limits. Accurate fuel gauges enable users to discharge batteries to their limits with confidence, Without having to worry about damaging the cell. GPIO, Short for General Purpose Input/Output, Is an interface used to connect electronic devices and microcontrollers, such as diodes, Sensors, Displays, etc.
The Battery Management System (BMS) is the cornerstone of electronic control in electric vehicles. Without this crucial system, The charging, discharging processes, And the overall lifespan of the power battery would be severely affected. If we compare the battery to a squadron of soldiers, The BMS system is like both the strategist and the commander, Enabling electric vehicles to achieve maximum efficiency in practical applications. Through the BMS, electric vehicles can control and manage the battery efficiently. Each battery operates within a safe range, Avoiding problems such as overcharging, Over – discharging, and thermal runaway. Due to the relatively low capacity of individual battery cells, Numerous cells are integrated into modules, And multiple modules make up a complete battery system. Usually, a battery system consists of hundreds or even thousands of individual cells. The BMS plays a crucial role in ensuring that each cell operates within the proper range. In other words, the BMS is a key element in maintaining optimal performance. This also highlights the significance of an EV BMS manufacturer. They play a critical role in developing and supplying these essential systems for electric vehicles.
Our Products Have Undergone Verification In The Market And By Global Customers. They Are Applicable to Diverse Usage Scenarios And Can Operate With high efficiency and remarkable resistance to damage.
This is the fundamental function of a BMS. It closely monitors the state of each cell using various parameters:
This parameter reveals a wealth of information including a cell’s total voltage, the combined voltage of the battery, As well as the maximum and minimum cell voltages.
It showcases the average temperature of individual cells, The intake and output temperatures of the coolant, And the overall temperature of the battery.
This indicates the battery’s current charge level, Giving users an idea of how much power is available.
Presented as a percentage of the original capacity, It shows the remaining battery capacity, Helping users assess battery degradation.
Considering factors like current usage, temperature, etc., This parameter reveals the amount of power accessible for a specific period.
Determined by comprehensively analyzing all parameters, It assesses if using the cell poses any risks.
These are crucial for maintaining optimal battery conditions.
Monitoring the flow of current in and out of the cell provides essential data for battery management.
Calculating the energy delivered since the last charge cycle helps in understanding battery usage patterns.
Measuring the battery’s internal impedance provides insights into the cell’s open – circuit voltage.
This determines the charge in Ampere – hours delivered or stored in a cell, Enabling the assessment of cell efficiency.
Tracking the total energy delivered and the operating time since the battery started being used gives a comprehensive view of battery performance.
Tracking the total energy delivered and the operating time since the battery started being used gives a comprehensive view of battery performance.
Manager:Nora Zeng
Wechat :15770741413
Whatsapp/Tel :+86-15770741413
E-mail:sales6@klspcba.com
Copyright © 2023 Shenzhen Kinglisheng Electronics Co., Ltd All rights reserved.